Are you ready to dive into the alluring world of aluminum extrusions? Brace yourself, because we’re about to explore the captivating differences between three seductive variants: Lite, Regular, and Heavy-Duty.
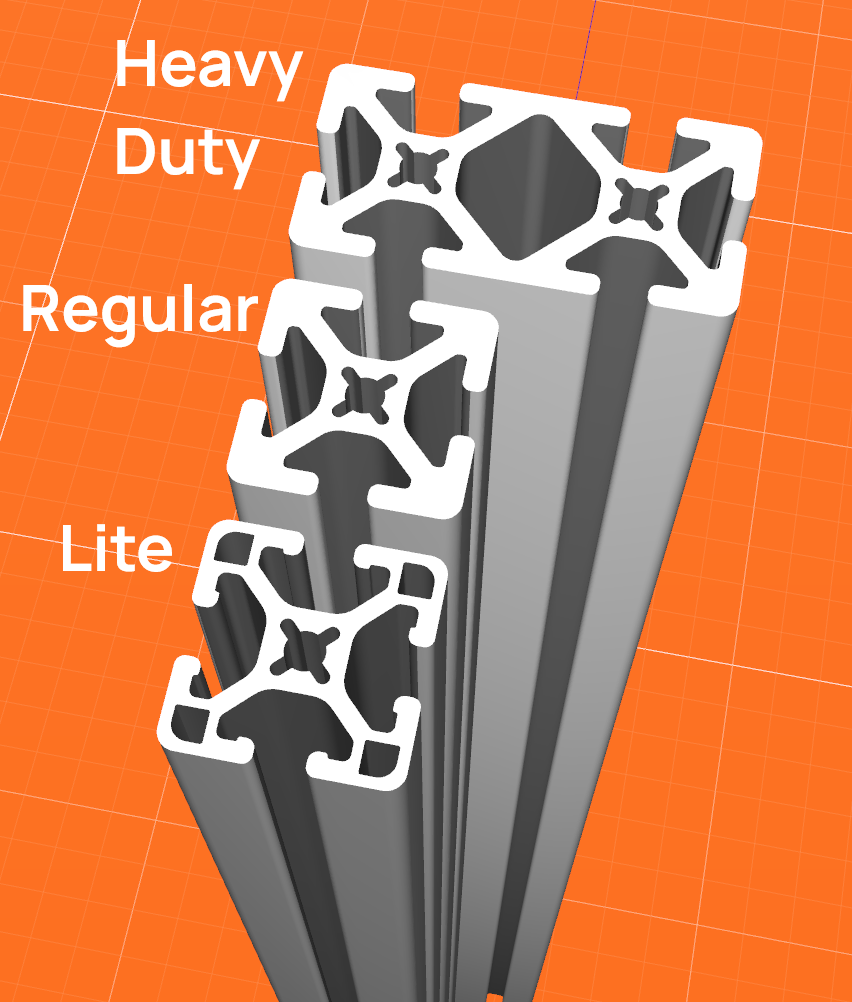
- Lite: Picture Lite extrusions as the seductive whispers of the aluminum extrusion world. Behind their sleek exterior lies a difference in internal thickness that gives them their lighter nature. While their internal structural members are slightly slimmer than Regular extrusions, lite extrusions look identical to regular extrusions from the outside. The difference is only noticeable from the cut end, showing their lighter and more affordable internal gussets. Their weight may be lighter, but they still holds their ground, making them perfect for applications that require a touch of affordability with a healthy dose of strength.
- Regular: These are the main attraction at the aluminum party. With a much thicker internal thickness, these extrusions possess a robust structural prowess. They are versatile and offer a blend of strength and elegance that leaves us breathless. Their seductive charm lies in their ability to handle a wide range of applications without compromising on strength, style or grace.
- Heavy-Duty: Prepare yourself for the alpha males of the aluminum extrusion realm. These may still have the same internal thickness of Regular extrusions, the Heavy-Duty structural members win out simply because they are twice the height of Regular extrusions. Doubling their height more than doubles their strength, making them perfect for projects where raw brute strength is desired. Whether you’re constructing sturdy frames or building robust structures, Heavy-Duty extrusions will ensure your creations stand tall amidst the competition.
Load Strength Calculations
To make the most of your aluminum extrusions, it’s essential to estimate their load-bearing capabilities accurately. Below we will show you the calculated deflection for different loads on a set length for the Lite, Regular and Heavy-Duty extrusions. We will use the length of 80″ as that’s the longest structural member we have in any of our current designs.
200 lbs | 300 lbs | 400 lbs | 500 lbs | |
Lite | 1.2″ – 30 mm | 1.7″ – 44 mm | 2.3″ – 58 mm | 2.9″ – 73 mm |
Regular | 0.9″ – 22 mm | 1.3″ – 32 mm | 1.7″ – 43 mm | 2.1″ – 53 mm |
Heavy-Duty | 0.1″ – 3 mm | 0.2″ – 5 mm | 0.2″ – 6 mm | 0.3″ – 8 mm |
This simple assessment shows the strength of an individual structural member, secured at both ends, under a static load with no assistance from other structural members. When you add other structural components, the rigidity and overall strength begins to compound, creating very sturdy and robust assemblies. These bed systems are reliant on all the individual structural parts, and become much stronger when connected together than the above table demonstrates. The load maximums described in the product descriptions are based on modelling the structure in it’s illustrated form. Any changes you make to the design or structure, will have an effect on it’s overall strength. This is why it’s important to always reassess the load strength after you make changes. You can learn more about that process in our How to Guide: A Playful Guide to Assessing Extruded Aluminum Load Maximums.
Conclusion
In the enthralling universe of aluminum extrusions, hopefully we have illustrated the distinct personalities of Lite, Regular, and Heavy-Duty variants. While Lite extrusions whisper with delicate prowess, Regular extrusions strike a balance between strength and style. However, it is the Heavy-Duty extrusions that conquer the scene with their towering strength and undeniable stability. So, with your newfound confidence, embrace the captivating allure of aluminum extrusions, and let your exploration be fearless in its strength and beauty!